Failure Analysis Service for the Integrated Circuit (IC) and Semiconductor industries
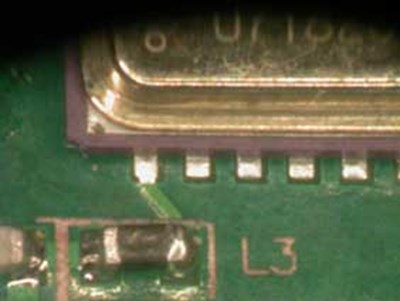
Design and fabrication failures are unfortunately an inherent part of the microelectronics business, where complexity is growing rapidly. Failures can occur throughout the product's life cycle, such as technology or product development and qualification, yield learning, reliability improvement, system manufacture, and field application. The impact of such failures ranges from consequential to catastrophic. While we expect failures during reliability stressing or yield learning on a new technology, mature programs and parts qualified for sale and field application demand competitive quality and reliability levels. Failures during these later phases of production need immediate analysis and corrective action.
Whether anticipated or sudden, failures can have a severe business impact. Because narrow market opportunities often drive shortened product cycles, companies need to understand failures and take corrective actions quickly. Electrical characterization, statistical analysis, signature analysis, and process experiments can provide important clues that allow us to infer the cause of failure. But only full root-cause physical failure analysis can provide the incriminating evidence necessary to correct problems with confidence: the picture worth a thousand words.
The crucial element of failure analysis is fault localization, a task for which both hardware and software techniques exist. Trends toward denser circuits and more sophisticated packaging, however, are limiting physical access to internal chip circuitry and thus diminishing the effectiveness of hardware-based diagnostics.
IC FAILURE ANALYSIS is the process of determining the physical root cause of component failure, given the electrical failure mode and characteristics. To accomplish this, it is necessary to combine a series of electrical and physical steps aimed at localizing and identifying the ultimate cause of failure. Due to the widely varying nature of components, failures, and defect mechanisms, a typical analysis could involve many loops between various steps, such as:
- Optical Inspection
- X-ray
- Scanning Acoustic Microscopy (SAM)
- Electrical Characterization
- Time Domain Reflectometry
- Dye and Pry
- Decapsulation
- Global Isolation
- Deprocessing
- Cross-Sectioning
- Scanning Electron Microscopy (SEM)
- Focused Ion Beam (FIB)